Extruder safety technical operation procedures
2019-09-04
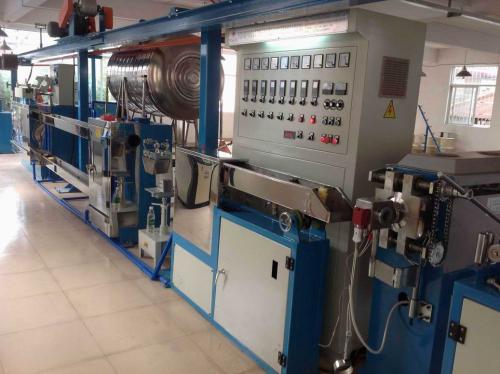
Extruder safety technical operation procedures
1. The operator must be familiar with this procedure, and after passing the examination, wear protective equipment before operating the equipment.
2. Production preparation
1. Before starting the machine, the operator should check the lubrication, transmission, electrical control and other conditions of the various parts of the equipment. If problems are found, they should be found in time to solve the problem. All kinds of production tools should be complete, and the measuring tools should be proofread accurately.
2. Select the mold according to the requirements of the product, and adjust the mold spacing.
3. To start the heating system 2-3 hours in advance, the temperature of each section should be adjusted according to the process regulations to prevent the temperature control from being too high or too high.
4. Before the production, the quality of the semi-finished products should be inspected according to the process regulations. There should be no oil, water, or excessively disordered wiring. Check the engineering record card, pay attention to the operation items, and have the certificate of the previous process inspection on the label. Can be produced.
5. Prepare the appropriate production reel according to the length of the product, and check if the reel has a hole.
6. Prepare the traction rope and test the oil pump pressure, air pressure, traction speed, take-up and take-up line rotation, automatic feeding device, heating control system, electrical switches of various departments, water circulation and so on, confirm no problem. Can drive production.
3. Boot
1. Add qualified plastic into the hopper, open the inserting plate, start the screw to continue running the glue. The operator should pay attention to the feeding situation, observe the screw pressure, and pay attention to whether the screw gear box is abnormally in the barrel. At this time, the operator does not Leave the machine to prevent problems.
2. After the plastic is extruded from the outer die, it is necessary to observe the plasticization of the plastic. When the plastic is about to be plasticized, the mold is adjusted, and the thickness of the plastic is adjusted evenly to prevent the deviation of the plastic layer.
3. Sampling according to the process regulations to check the thickness of the plastic, and check the quality of the plastic after extrusion, such as pores, trachoma, surface plasticization, enamel and other impurities, cross-section should not be visible to the naked eye.
4. All the conditions are normal. After the production can meet the requirements of the process regulations, the personnel should be actively organized to start the machine, and the division of labor should be carried out when driving.
5. Wear the lead wire, the semi-finished product and the lead wire should be firmly connected to prevent the pull-out, the joint should be tightly packed to prevent the cable core from entering the water, and the joint should be seen by the special person.
6. Pay attention to the following points in the normal production process:
a. Product quality
b. Mechanical operation of equipment
c. Control of the heating system
d. Changes in screw and traction speed
e. To achieve three diligence: diligently measure the outer diameter, check the quality, and observe the equipment.
7. Record the label, track record, process list and other records.
4. Parking
When parking, please inform the line-receiving personnel to prevent the tension of the receiving line from being too large. After stopping the vehicle, remove the mold in time, open the screw at the contact between the machine head and the fuselage, turn off the inserting plate of the feeding hopper, push the machine head out, run the net. Plastic inside the fuselage, organize personnel to clean the nose.
1. Stop the machine if you encounter the following conditions:
a. Shut down the machine head in time after the completion of the production task
b. When the temperature is too high, it will cause the plastic to burn, and the head and screw should be cleaned.
c. Long downtime to clean the machine head
d. There are other reasons for downtime, such as power outage, water stop, waiting for the line, waiting for the disk, equipment or personal accidents should be cleaned
2. The machine head and screw should be cleaned up, and the machine head should be installed after cleaning.
3. Take notes and prepare for the next shift. For example: molds, production trays, semi-finished products, etc.
4. After shutdown, check the power supply, water source, gas source, and various parts of the equipment. After confirming that there is no problem, turn off the power, and then leave the machine.