Preheating and cooling of wire and cable extruder
2019-09-04
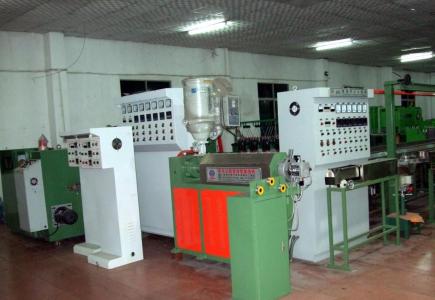
1. Preheating of the conductor
When the wire and cable are pushed out, the molten material is in contact with the cold conductor. Due to the quenching of the material, the extruded layer has strain residual. The residual strain is cooled and solidified before it is slowed down, and the finished product will shrink, elongate, age and dense. Poor problems such as sex, especially for products with very poor insulation. If the conductor is preheated at an appropriate temperature, there is no quenching when it comes into contact with the molten material. If it is not checked, the quality of the extrusion can be improved, and the conductor is dried and cleaned. Quite the effect. (The preheating temperature of the conductor is directly controlled by the extraction speed and the wire diameter, that is, the smaller the wire diameter, the higher the temperature, and the faster the wire speed, the higher the temperature)
The main equipment used for preheating the conductor is the copper wire preheater. The copper wire preheater is available in several models and can be selected according to actual needs.
2. Cooling sink
The cooling conditions have a great influence on the characteristics of the finished product. The operation should be cautious. When the original insulation or the coating is extruded, under the rapid cooling conditions, the surface will be solidified first, while the inner layer will be cooled slowly. Due to the different shrinkage, bubbles will be formed. Poor, such as sequential cooling, can prevent this shortcoming, so the use of segmented cooling, that is, near the eye mold end, the water temperature of the sink is held at about 80 and then the temperature is gradually reduced after the segment, to the end of the sink is normal temperature, this cooling The method has a very good effect on the improvement of the finished product characteristics.
Generally, when the thickness is extruded, as long as the warm water (about 40 degrees) is used at the beginning of the water tank, it has a good effect. The thin layer is squeezed out of the sequential cooling to improve the characteristics of the finished product, and the thin line is extruded at a high speed, usually still divided by cold, and the air cooling can be adjusted. Distance.
When the cable is pulled out, it is not sufficiently cooled to be flattened when it is taken up, or the printing is overprinted (ink material and cooling effect are possible), so how to make the most appropriate cooling is an important step.
The cooling water tank can be selected according to the size of the wire diameter and the actual requirements. The general water tank has a double-layer water tank, a single-layer water tank, and a U-shaped water tank.